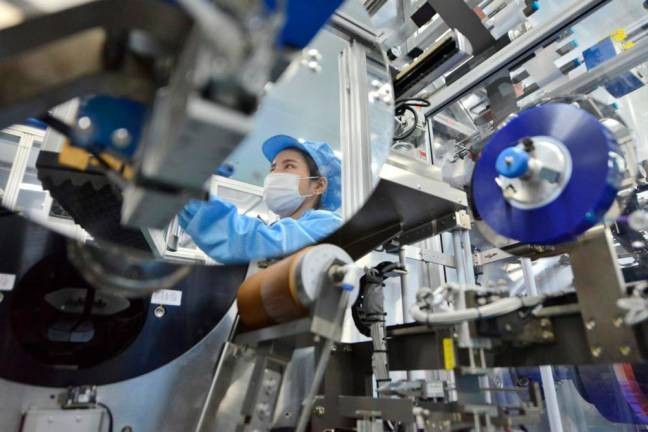
COVID-19 has caused unprecedented disruption to economies worldwide that will leave a lasting impact for years to come. Globally, the supply chain has shown vulnerabilities which has been severely elevated amid heightened uncertainties from the pandemic. Whilst locally, the services and manufacturing sectors being key contributors to Malaysia’s economy have taken the brunt of the hit.
As highlighted by Bank Negara Malaysia (BNM) governor Datuk Nor Shamsiah Mohd Yunus recently in BNM’s Annual Report, Malaysia has had to face a number of surprises this year, and it is hard to predict what might happen next.
In BNM’s outlook and policy 2020 statement, it is stated that the pandemic is simultaneously causing demand and supply shocks through supply-chain disruptions and weaker demand. The global Purchasing Managers’ Indices (PMIs) for manufacturing and exports, which demonstrated impending signs of recovery at the end of last year, spiralled downwards in the first three months of 2020 (graph demonstrates).
The impact from China’s extended production shutdown between January and March has evidently affected local businesses and manufacturers as they grapple with the domino chain of events.
Whilst prospects for global growth will depend on how fast the pandemic is contained and stopped, finding the cure to Covid-19 will be a lengthy process. Economies and businesses cannot wait. With desperation to find solutions, companies need to immediately rethink the way they do business, and to examine the entire supply chain.
Here are three ways to better survive a supply chain disruption and come out steadier than ever before.
1. Diversifying Risk – Multiple Supplier Sources Both Locally & Abroad
According to the research carried out by The Institute for Supply Management, nearly 75% of the companies it surveyed in late February and early March 2020 reported supply-chain disruption due to the coronavirus. Of that, 44% of the companies did not have a plan to deal with this kind of disruption.
The biggest learning for the business is not to rely on one or two suppliers but to have approved multiple suppliers for each of the items they procure, some of them closer to home and in emerging countries. Whilst most companies will still continue to look to China as their primary supplier, it would be prudent to consider a new ‘China +1” strategy for future supply chain needs.
Sourcing locally will help to revitalise the economy, reduce cash outflow from the economy, inject investments where it is needed at such a crucial time and support and grow local talent.
2. Technology is Integral to the Global Supply Chain
The pandemic has demonstrated how essential it is for all companies to obtain more visibility to see how disruption is affecting the entire supply chain. This allows businesses to adopt alternative plans such as developing routes to other suppliers.
Technology such as the Enterprise Resource Planning (ERP) application, integrating all the facets of a company as well as connecting customers and suppliers has never been more important. It helps businesses to identify supply chain exposure and manage or mitigate risks.
In this connected supplier environment, the impact of disruption is greatly reduced.
Next Generation ERP’s can be implemented in a short period of time, from as little as four weeks whilst the finance and distribution modules can be implemented in just two weeks. Smaller SMEs can also consider an affordable Cloud ERP solution with a fast-track
implementation programme. An ERP solution provides agility for the organisation and provides a platform for future proofing the business.
3. Prepare for the Rebound
What will separate organisations that thrive post-crisis with ones who don’t, will be whether or not they’re prepared for the rebound. Companies that are able to move more quickly than their competitors may capture a larger share of the pent up demand, solidify their relationships with their most important customers and even gain some new ones.
Pricing strategy will be an important consideration as businesses gradually transition back to normal—both to address normal supply-demand considerations, as well as to maintain profitability while logistics costs and potentially other costs, will likely be volatile.
The immediate focus for most companies would be improving visibility to supply chain risk in its own facilities, with direct suppliers and beyond. Getting this extended supply chain visibility will likely require a more digitised approach than many companies have been used to in the past.
Implementing solutions which leverage artificial intelligence and machine learning-powered platforms, incorporating a breadth of data using proprietary and subscription-based solutions to illuminate supply networks more quickly, to a level of detail that was previously thought to be impossible, should be a priority.
Future proofing one’s business is no longer an option
Unfortunately, there is no guarantee that the pandemic will come to a complete end in the near future. Experts also have predicted that such outbreaks may reoccur. Starting a business continuity plan for a supply chain of the future is necessary as different countries will hit peak disruption at different times, as seen today.
Manufacturing companies especially, will need to adopt this ‘new normal’ of supply chain agility and implement digital and automated manufacturing capabilities paired with strong manufacturing excellence to ensure their continued survival in the ‘next normal’ world, post Covid-19.
Whether it is another pandemic, trade war, terrorism or some never seen before event – future proofing one’s business is no longer an option but mandatory.
Source : https://www.thesundaily.my/business/surviving-the-global-supply-chain-disruption-EL2278134