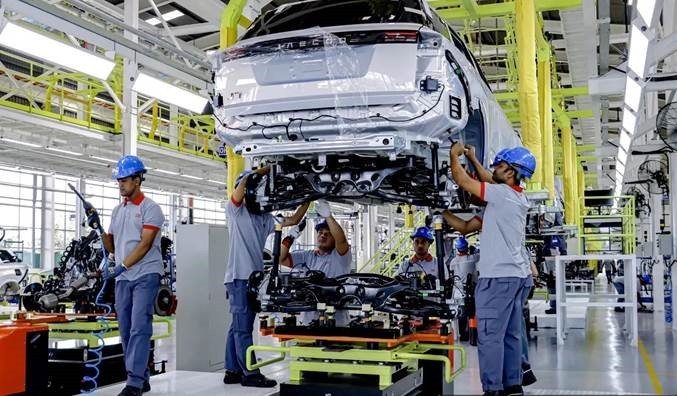
Image credit: FMT
KUALA LUMPUR, July 15 (Bernama) -- Malaysia's potential in becoming an automotive hub for ASEAN not only lies in strategies to boost car exports; it also hinges on the increased export of parts and components.
In order to achieve this, Malaysian automotive and parts companies must persevere to increase exports of cars significantly in order to achieve economies of scale and enable auto parts to be sold at more competitive prices.
Increased sales volumes can reduce production costs and subsequently component prices, making them more competitive than those in regional and neighboring countries where auto parts are cheaper due to their high sales volumes.
Car manufacturers, auto industry researchers and economists believe that these endeavours are crucial to establishing Malaysia as a regional automotive hub for ASEAN and taking advantage of the region's close to 700 million consumer base.
“We urge original equipment manufacturers (OEMs) to not only export cars but also parts and components, thereby enhancing the overall competitiveness of the Malaysian automotive industry,” said Azrul Reza Aziz, Malaysia Automotive, Robotics and IoT Institute (MARii) chief executive officer to Bernama.
He said this in response to reports that Malaysia's supply chain costs are 30 per cent higher than China’s, and 10 per cent costlier than Thailand’s.
Azrul Reza pointed out that it is essential to recognise that these costs varies significantly, depending on each company's cost structure, car model, and supply chain ecosystem.
He highlighted that companies may have different levels of maturity in their supply chains, which impacts their overall cost efficiency.
Malaysia undoubtedly has a lot of catching up to do, as, despite marking significant growth, its record high total production volume (TPV) was only 775,000 vehicles, compared to China’s TPV which stood at around 30 million vehicles and Thailand's at 1.8 million vehicles.
Azrul Reza said Malaysian companies must transform by embracing digital advancements, leveraging Industry 4.0 (IR4.0) technologies to address the challenges.
This is crucial as the country aims for carbon neutrality by 2050, focusing on the development of electric vehicle (EV) components, autonomous vehicles (AV), and Internet of Things (IoT) components.
“Given the constraints on purchasing raw materials in bulk due to cost implications and the added expenses of stock handling and maintenance, digital solutions offer respite in terms of immediate insights and resolutions.
“Furthermore, digital solutions enhances efficiency and effective improvements in research and development, notably through the utilisation of computer-aided engineering and additive manufacturing technologies,” he said.
Meanwhile, Malaysian Automotive Association (MAA) president Mohd Shamsor Mohd Zain noted that China and Thailand’s domestic pool of population, vehicles, and maintenance networks are considerably larger than Malaysia’s.
Their reduced reliance on exports means that their vendors are less vulnerable to fluctuating exchange rates.
Similarly, such costs are largely driven by the push and pull of demand and supply, he said.
“Although Malaysia has a relatively mature automotive supply chain, dating back more than 50 years, the cost of setting up, or refreshing component manufacturing with new technology is very high.
“The most effective way to justify these investments is for Malaysia to position itself as an export hub,” he said.
Mohd Shamsor said the local automotive industry needs to build its competencies in terms of quality, affordability and productivity in locallyproduced parts by expanding the export volume and ramping up OEMs’ capacities.
He added that manufacturers often have different perspectives on how their business models are structured, and cost is only one consideration among many.
Source: https://www.bernama.com/en/business/news.php?id=2317574